Login
MyFFonseca
If you do not have an account MyFFonseca, please register and get access to exclusive content to registered users!
Create registryLogin
MyFFonseca
If you do not have an account MyFFonseca, please register and get access to exclusive content to registered users!
Create registry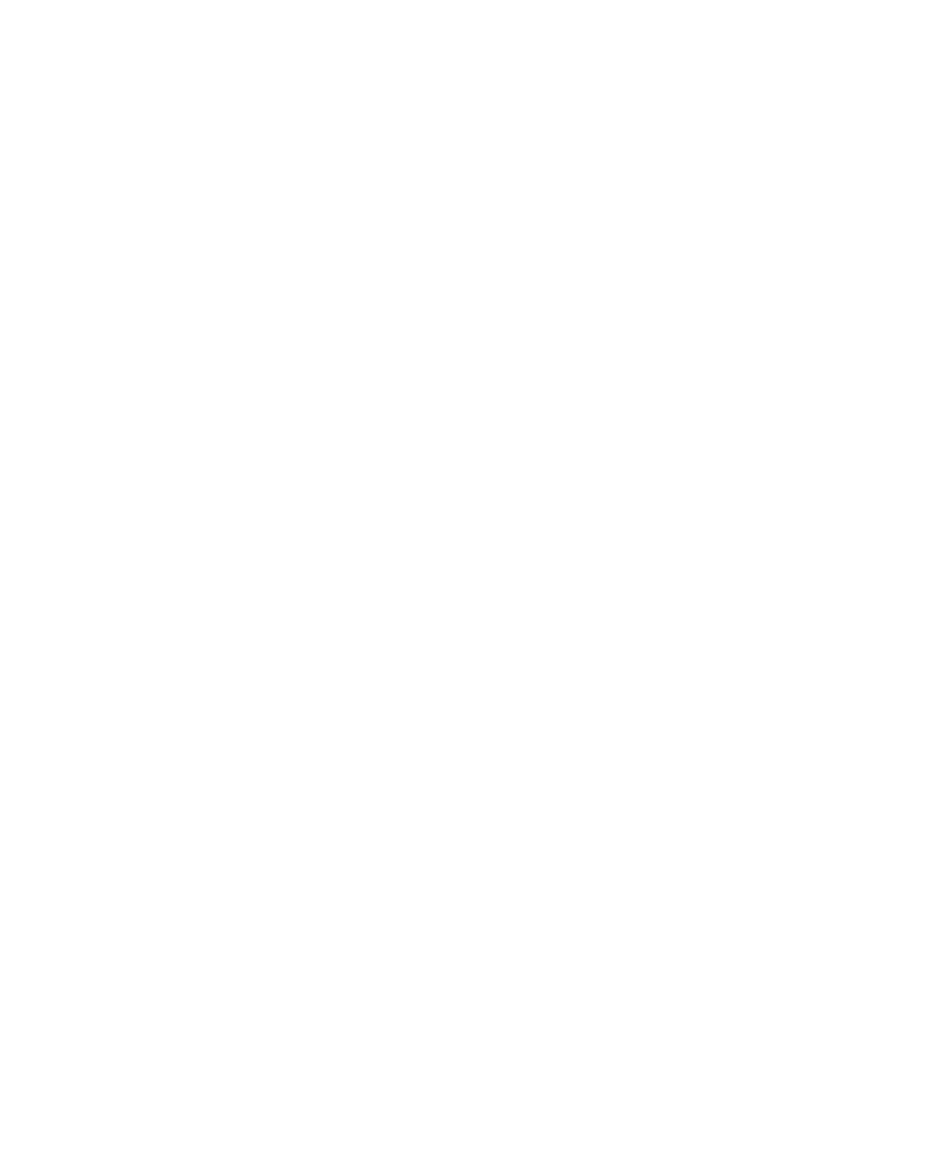
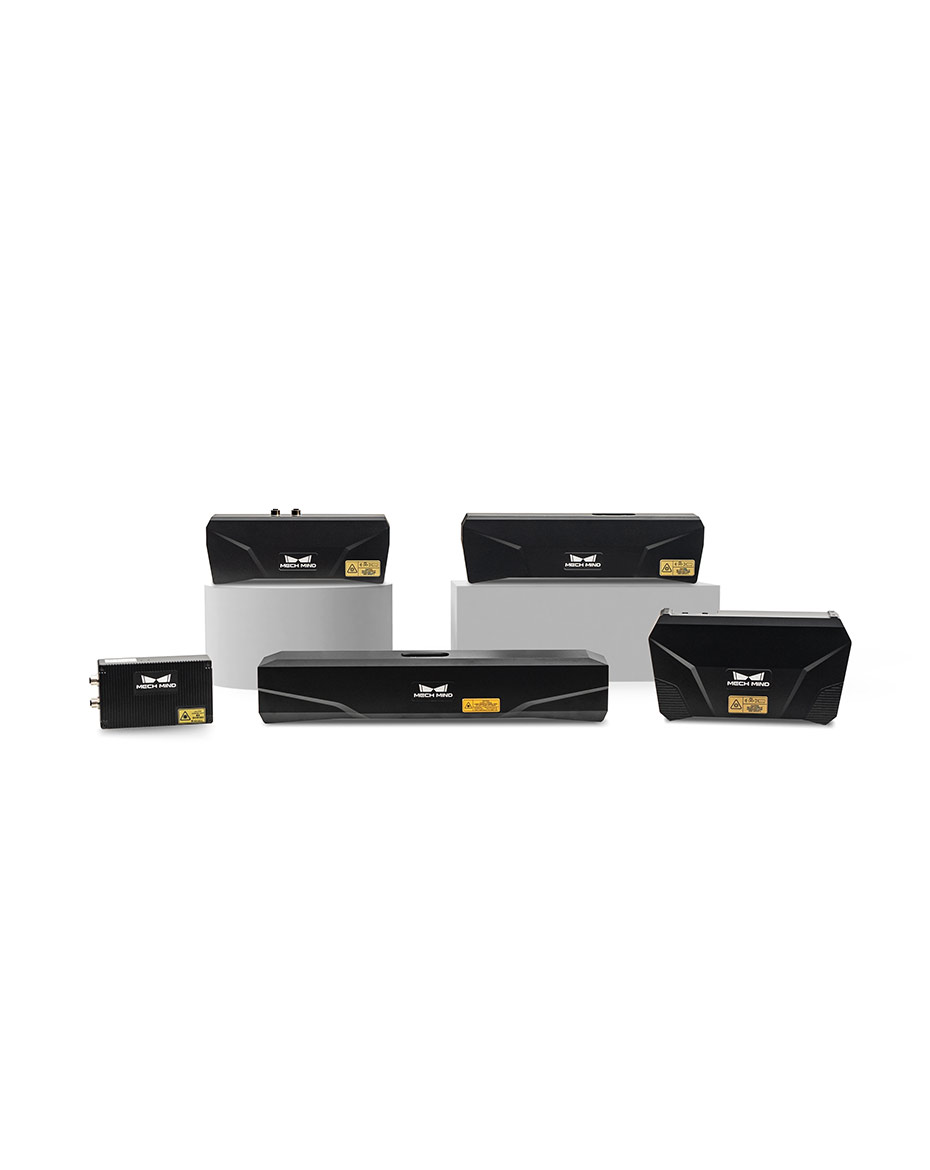
3D vision with artificial intelligence – Mech-Mind
Empower industrial automation of the most challenging tasks, including bin picking, depalletizing & palletizing, assembly and more.
SOLUTIONS: All-in-one AI + 3D intelligent robot solutions;
PRODUCTS: High-performance industrial 3D cameras and intelligent platform software;
POINT CLOUD: High-quality 3D data of a broad range of objects;
USE CASES: 3000+ real-world cases.
SOLUTIONS: All-in-one AI + 3D intelligent robot solutions;
PRODUCTS: High-performance industrial 3D cameras and intelligent platform software;
POINT CLOUD: High-quality 3D data of a broad range of objects;
USE CASES: 3000+ real-world cases.
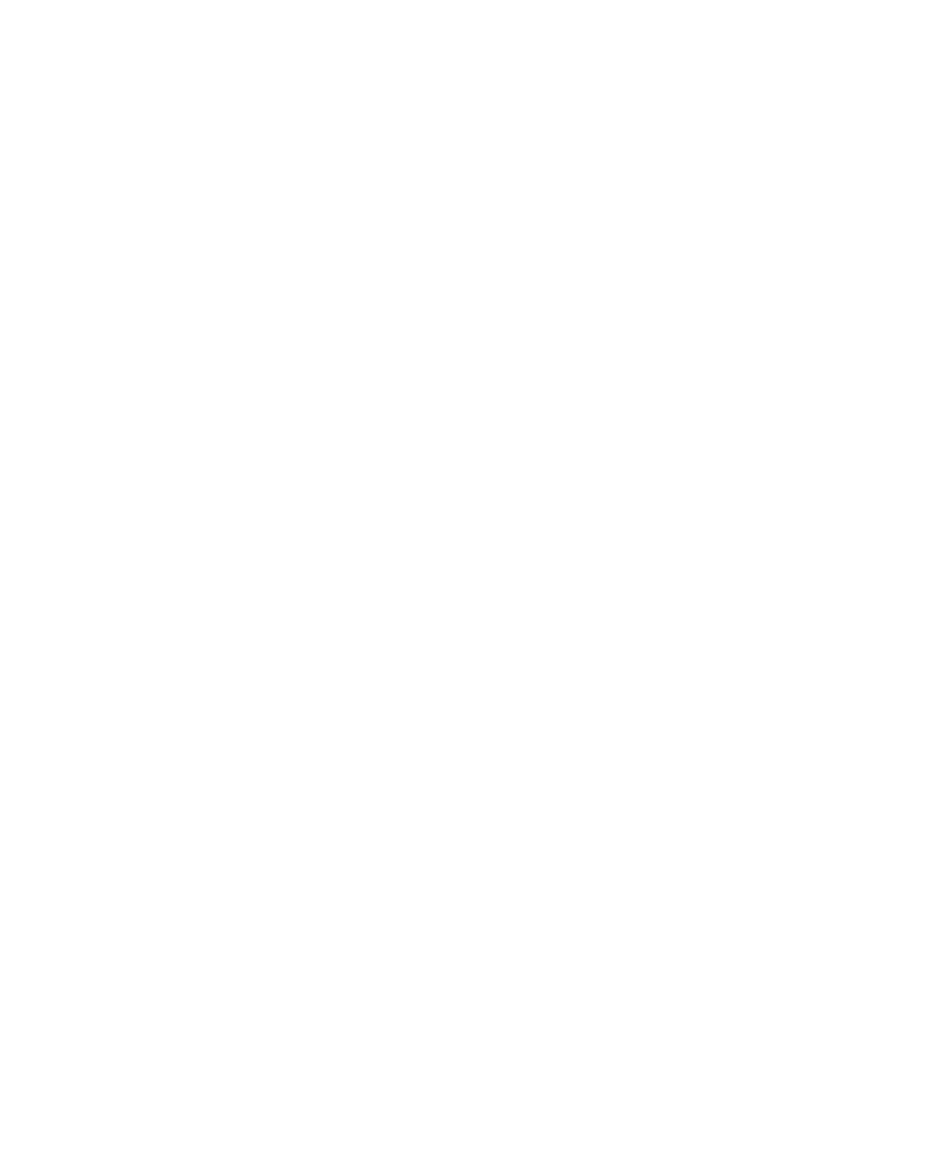
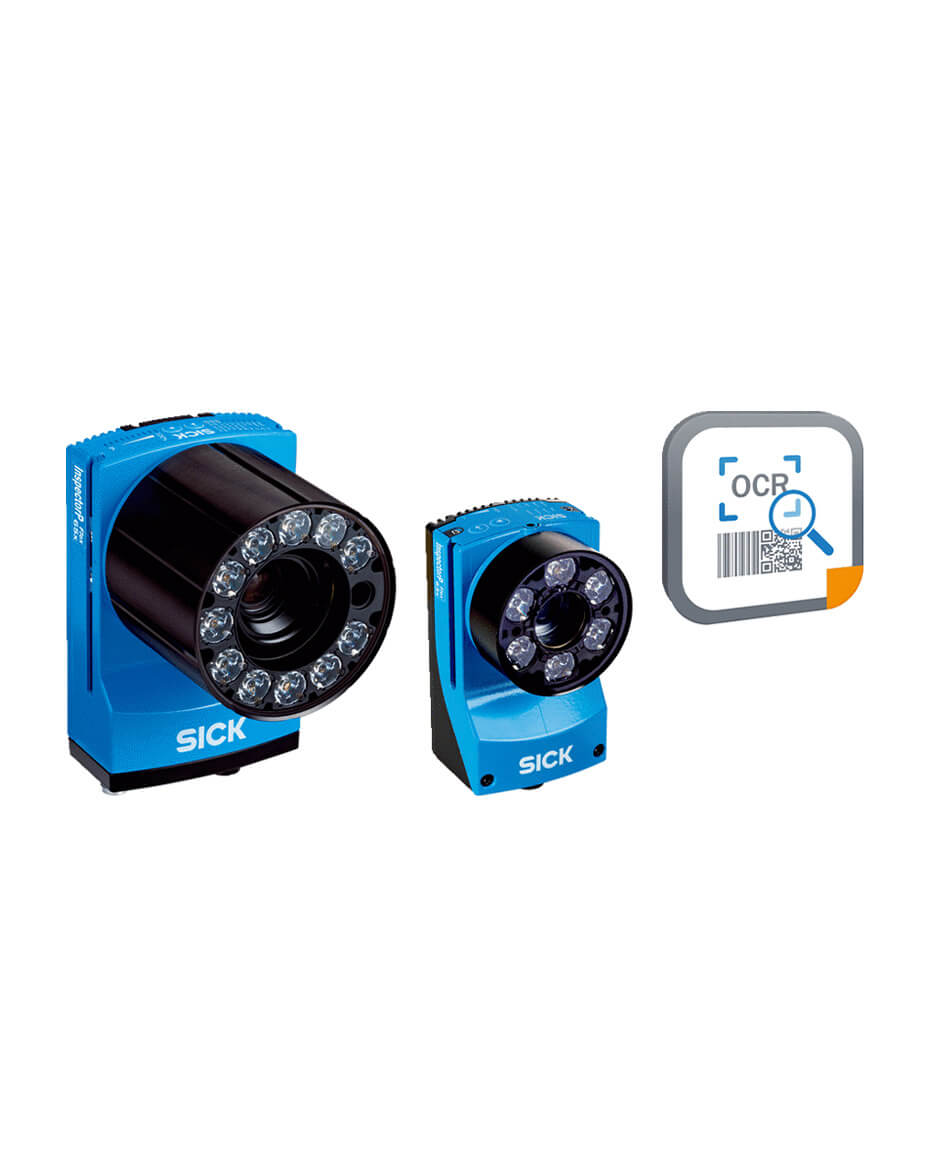
Label Checker system solution – SICK
Accurate product labeling is essential for ensuring overall process quality. The Label Checker quality control system is the right choice for such applications: It checks countless product label features, making sure that labeling processes run smoothly and efficiently at all times. This results in very high product quality and productivity.
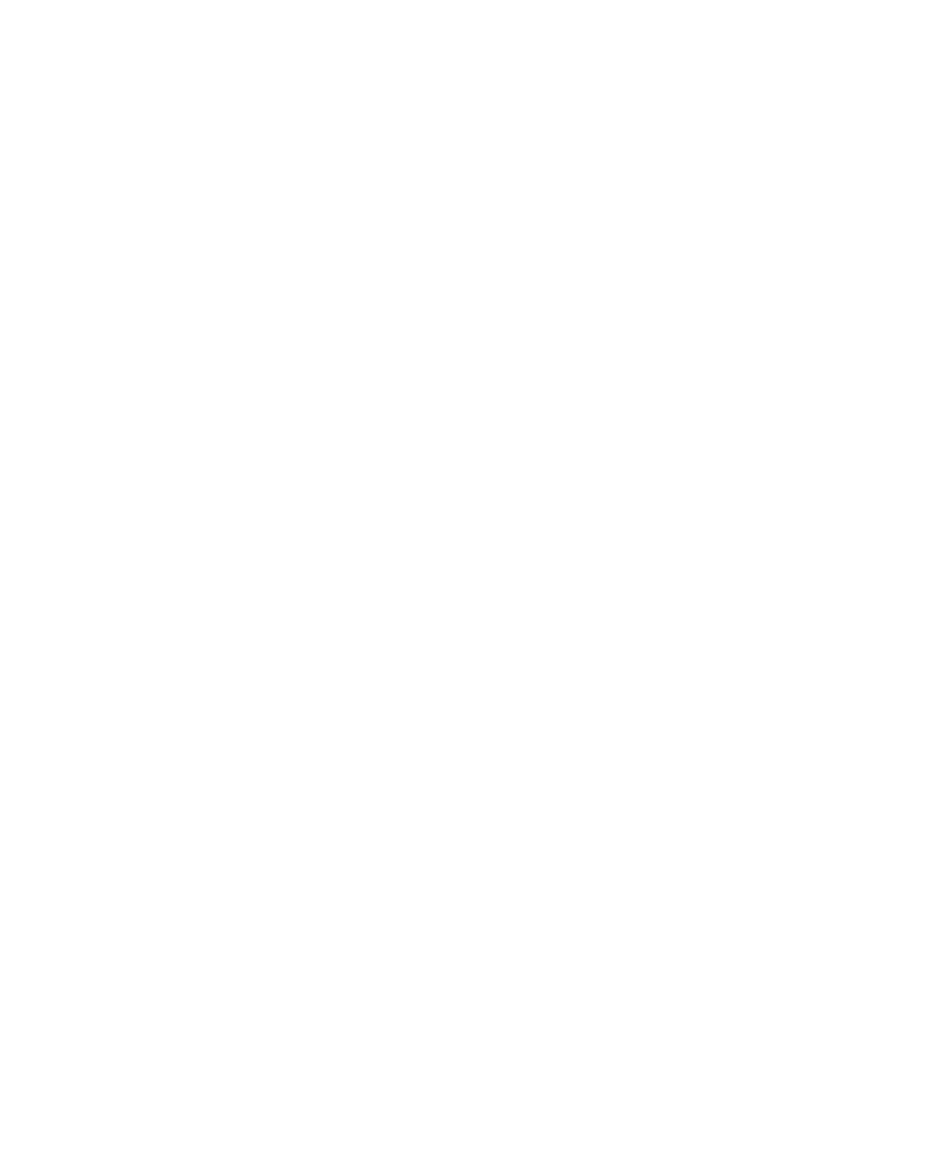

Part localization for bin picking - SICK
Pick, sort and place based on 3d and color featuring artificial intelligence.
Robot guidance systems | 3D machine vision: with the boom in e-commerce, warehouse throughput needs to scale up. A wide variety of items needs to be handled at high speed. Floorspace and worker availability are limited resources.
Fully automated picking robots help to increase pick-and-place accuracy and speed with 24/7 uptime and only a small footprint.
Robot guidance systems | 3D machine vision: with the boom in e-commerce, warehouse throughput needs to scale up. A wide variety of items needs to be handled at high speed. Floorspace and worker availability are limited resources.
Fully automated picking robots help to increase pick-and-place accuracy and speed with 24/7 uptime and only a small footprint.
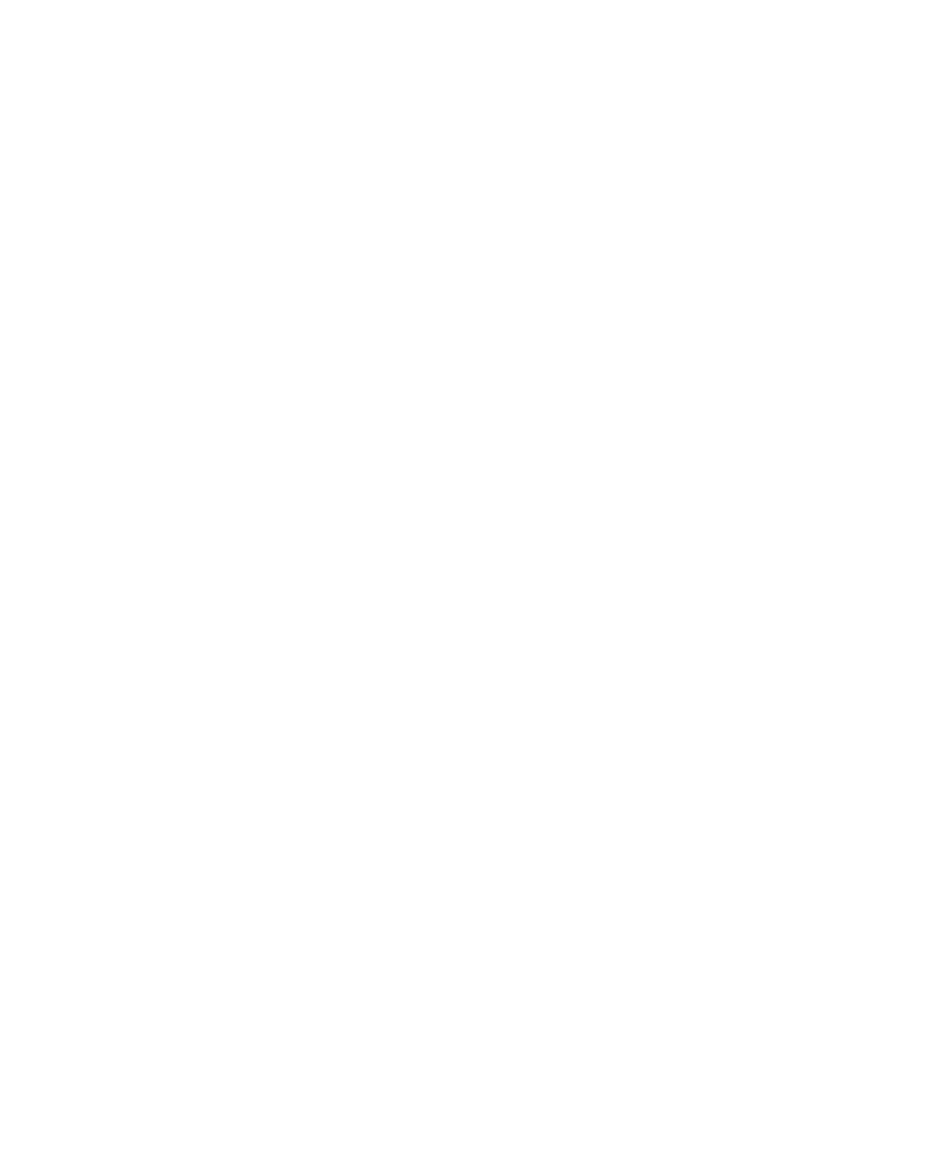
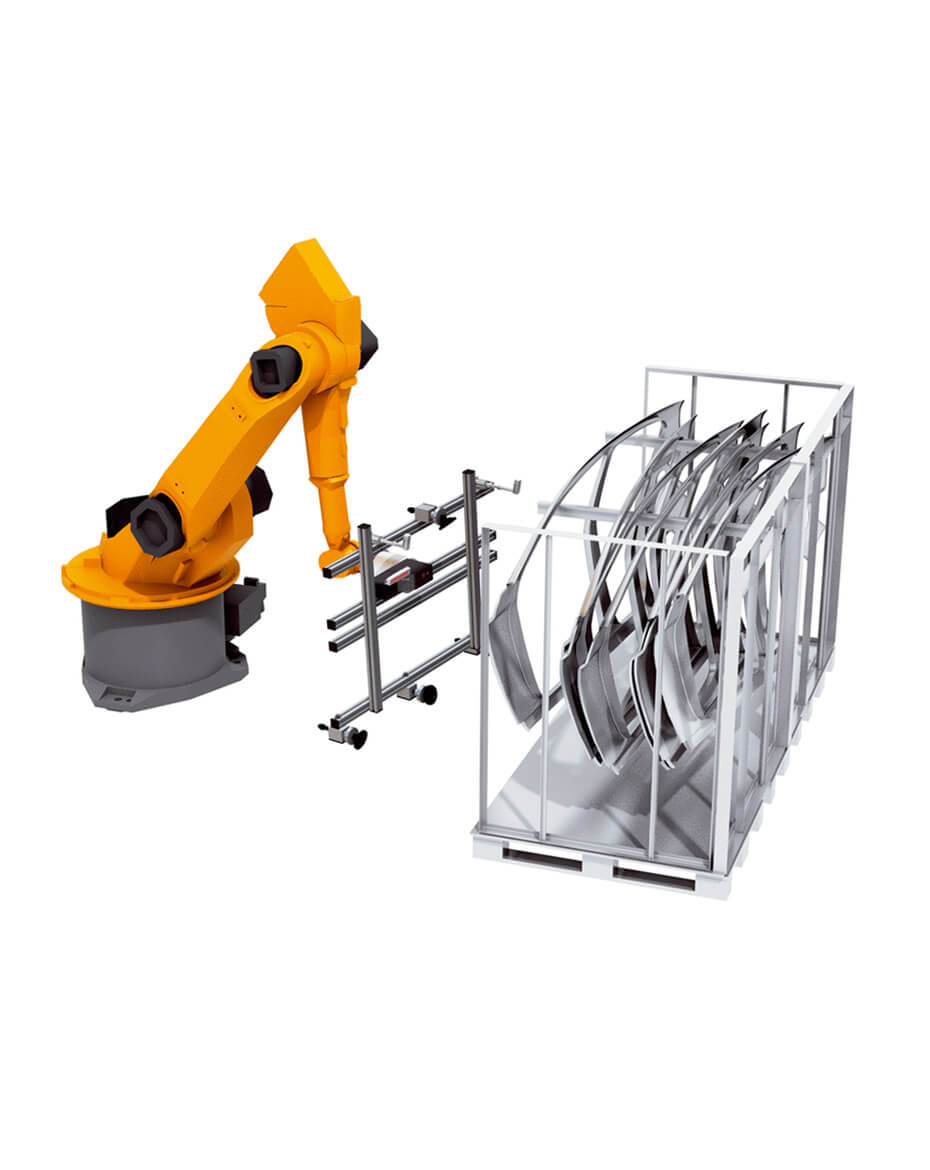
PLR 3D localization of parts in carriers - SICK
Part handling is one of the most important applications for factory automation. The use of flexible robots for this task represents a cost-effective alternative to traditional manual and semiautomatic handling systems.
The PLR has been developed for robot automated part handling. It is a standalone device that includes all the localization functions, an easy-to-use robot interface, as well as all the functions necessary for rapid integration with the robot.
The PLR has been developed for robot automated part handling. It is a standalone device that includes all the localization functions, an easy-to-use robot interface, as well as all the functions necessary for rapid integration with the robot.
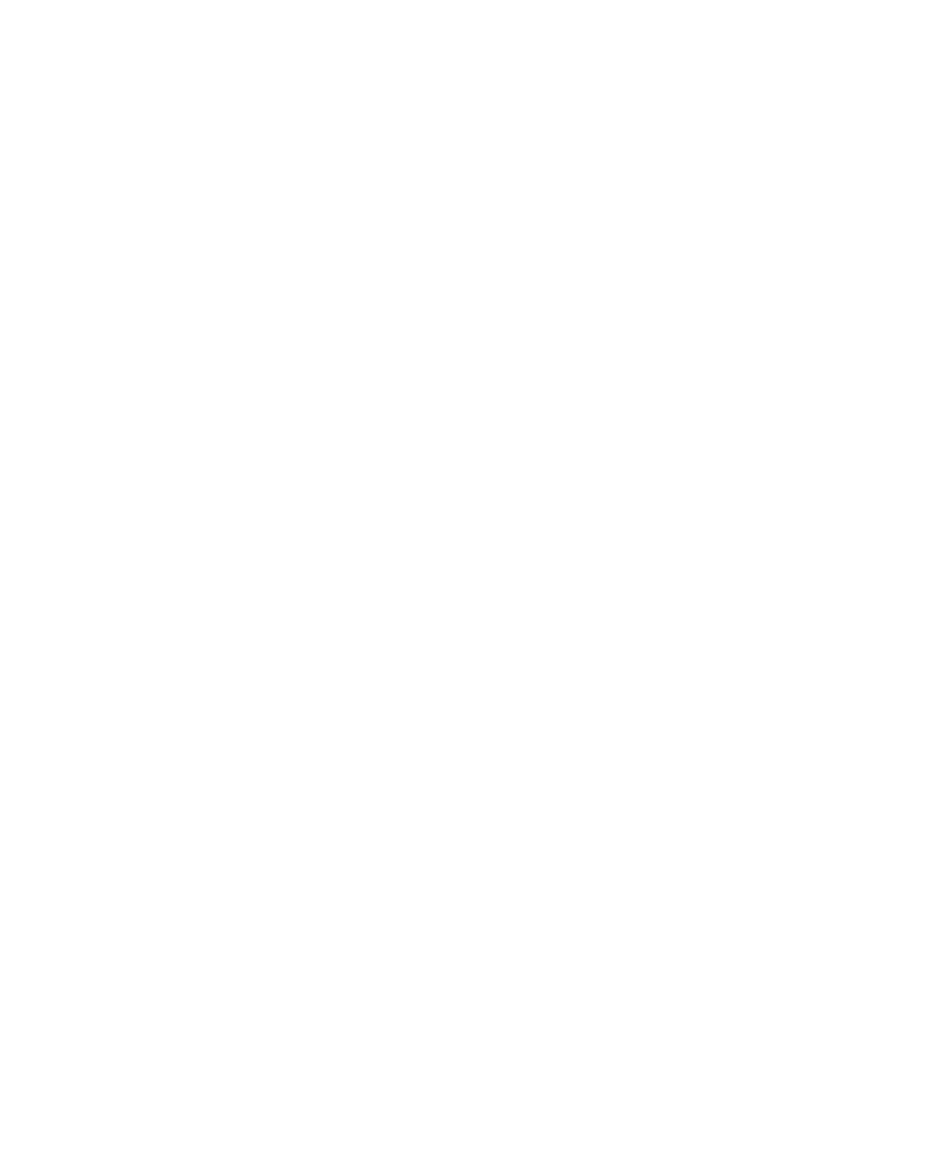
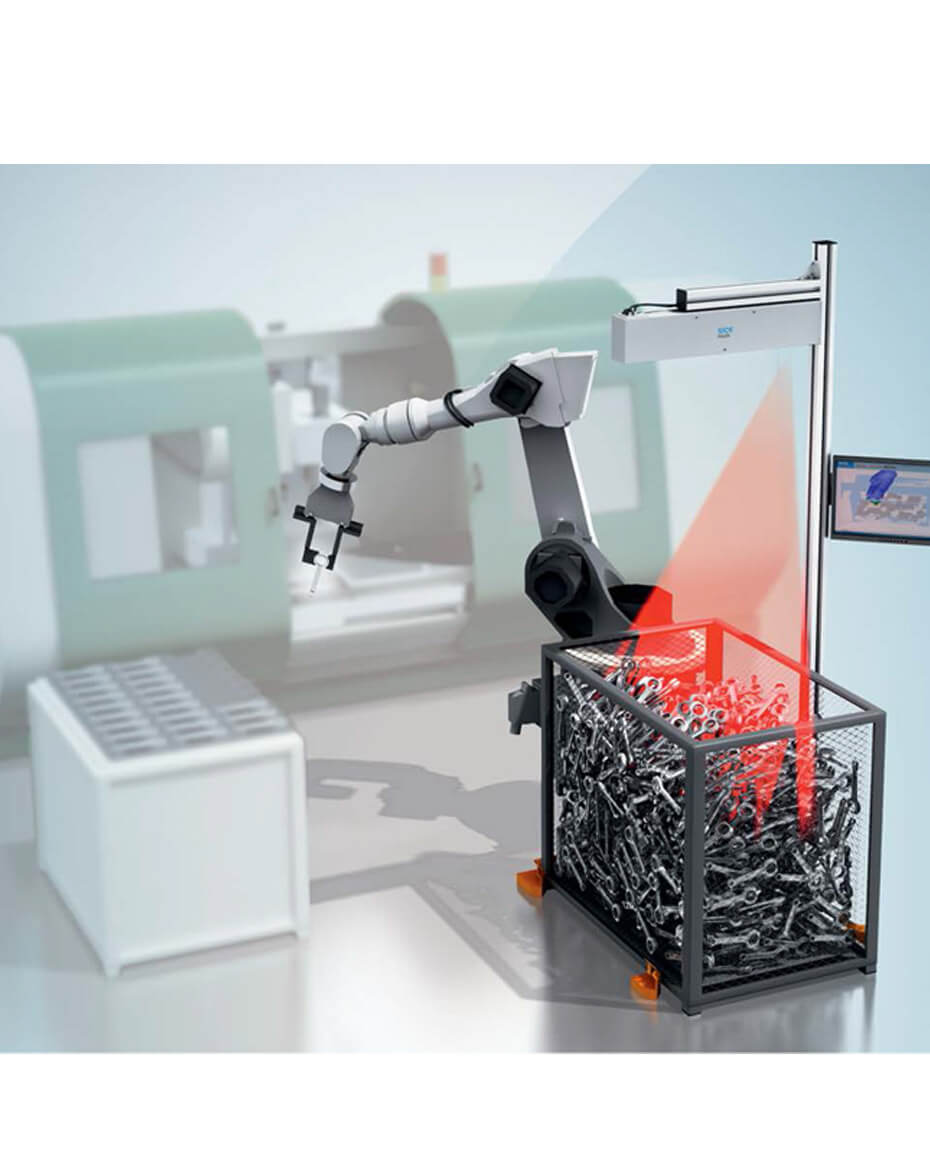
Vision system PLB - SICK
SICK'S PLB vision system is designed for precise localization of randomly orientated parts in bins and boxes. It enables the easy introduction of new parts into existing work cells and short part changeover time by using CAD-based 3D shape matching part localization software.
The PLB’s performance supports high production rates. The vision system consists of a 3D camera, part localization software and tools for easy integration and communication. The system’s advanced 3D camera ensures superior image quality and provides high immunity to ambient light. Field-proven tools and functions for calibration, communication with a robot and PLC, as well as checking for free gripping position, make it easier to integrate the system into production. The hardware and software are already integrated and pre-set for the application.
The PLB’s performance supports high production rates. The vision system consists of a 3D camera, part localization software and tools for easy integration and communication. The system’s advanced 3D camera ensures superior image quality and provides high immunity to ambient light. Field-proven tools and functions for calibration, communication with a robot and PLC, as well as checking for free gripping position, make it easier to integrate the system into production. The hardware and software are already integrated and pre-set for the application.
- 0
- 1